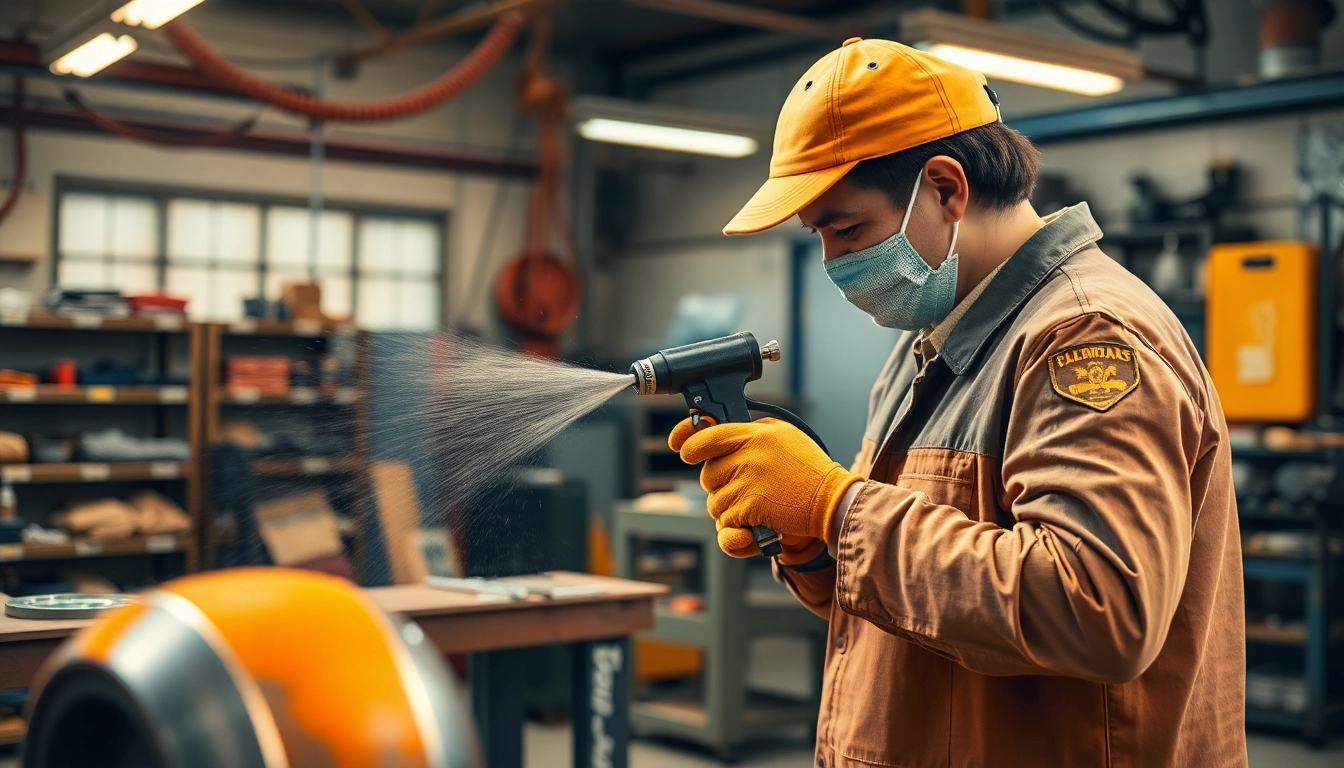
Understanding Powder Coating Basics
Powder coating is a specialized finish that applies a dry powder to metals, providing a durable, aesthetically pleasing surface. Unlike traditional paint, powder coating uses a unique process that results in a thicker, more resilient layer resistant to scratches, chipping, and fading. As a technique that has gained traction in industries ranging from automotive to home décor, understanding the fundamentals of powder coating is essential. For those interested in this versatile finishing process, powder coating presents numerous opportunities for customization and protection of substrates.
The Science Behind Powder Coating
At its core, powder coating involves a process that combines polymer resin systems with curatives, pigments, leveling agents, and flow modifiers. The powder is applied electrostatically and then cured under heat, causing it to fuse into a smooth, hard finish. The science behind powder coating relies on the principle of electrostatics — the fine, dry powder particles receive an electric charge as they exit the spray gun, making them adhere to the grounded metal surface. When heated, these particles melt, flow, and coalesce to form a continuous, durable film.
Benefits of Using Powder Coating
The advantages of powder coating over traditional liquid coatings include:
- Durability: Powder coatings are known for their high resistance to impact, wear, and corrosion.
- Variety of Finishes: A wide range of colors and finishes, including matte, glossy, and metallic, are available.
- Environmental Impact: Powder coating contains no solvents and generates minimal volatile organic compounds (VOCs), making it a more environmentally friendly option compared to conventional paints.
- Cost-Effectiveness: When considering the longevity and durability, powder coated surfaces can reduce maintenance and replacement costs over time.
Common Applications for Powder Coating
Powder coating is widely used across various industries. Some common applications include:
- Automotive Components: Wheels, bumpers, and chassis frequently undergo powder coating for enhanced protection and aesthetics.
- Furniture: Designers use powder coating for outdoor furniture due to its resilience against weather and UV rays.
- Appliances: Many household appliances employ powder coating to improve durability and aesthetic appeal.
- Architectural Elements: Railings, window frames, and other architectural features benefit from the protective qualities of powder coating.
Preparing Your Surface for Powder Coating
Before beginning the powder coating process, proper surface preparation is crucial to achieve the best results. The preparation phase typically involves cleaning, choosing the right powder, and utilizing the appropriate tools.
Surface Cleaning Techniques
Cleaning the surface to be coated is paramount. Common cleaning methods include:
- Sanding: Removing imperfections and ensuring a smooth surface.
- Degreasing: Using solvents to remove oils, grease, and contaminants that can hinder adhesion.
- Blasting: Techniques such as sandblasting or bead blasting create a textured surface that improves adhesion for the powder coating.
Choosing the Right Powder Coating Type
Different types of powder coatings are available, each with unique properties suited for various applications. The two main categories are:
- Thermoset Powder Coatings: Known for their hardness and chemical resistance once cured, these are ideal for industrial applications.
- Thermoplastic Powder Coatings: These can be re-melted and reshaped, making them suitable for applications requiring flexibility.
Essential Tools and Equipment for Preparation
To prepare a surface effectively, you need various tools and equipment, including:
- Blast Cabinet: For cleaning parts by removing contaminants through abrasive techniques.
- Powder Coating Gun: Electrostatic spray guns that facilitate the even application of the powder.
- Curing Oven: Used to heat the coated parts, allowing the powder to melt and cure properly.
The Powder Coating Application Process
The application of powder coating involves several specific steps to ensure a high-quality finish.
Step-by-Step Powder Coating Application
Here’s a simplified overview of the typical powder coating process:
- Preparation: Clean the surface thoroughly to remove any contaminants.
- Application: Use an electrostatic spray gun to evenly coat the surface with powder.
- Curing: Place the coated object into a curing oven at the specified temperature for a recommended duration.
- Cooling: Allow the part to cool down after curing, which solidifies the powder into a hard finish.
Common Mistakes to Avoid During Application
Even seasoned professionals can run into issues during the application process. Here are some common pitfalls to avoid:
- Improper Surface Preparation: Skipping cleaning phases can lead to adhesion failures.
- Inconsistent Coating Thickness: Failing to apply an even coat may result in patches or thin spots that are less durable.
- Incorrect Oven Temperature: Insufficient curing temperature can lead to poor finish while overheating can char the powder.
Post-Application Curing Process Explained
After application, the curing process is critical. Curing involves heating the coated item to a specific temperature, where the powder melts, flows, and then chemically reacts to form a hard, durable layer. The typical curing temperature ranges from 350°F to 400°F for 10 to 20 minutes, depending on the powder used and thickness of the layer.
Enhancing Durability with Powder Coating
To ensure optimal performance and longevity of powder-coated surfaces, understanding the curing process and maintenance tips proves invaluable.
Understanding the Curing Process
The curing process not only solidifies the coat but also enhances chemical resistance and thermal stability. Different powder formulations may require various curing parameters, and understanding these nuances can enhance the performance of the coating:
- Cross-Linking: This chemical reaction during curing provides improved chemical resistance and hardness.
- Thermal Stability: Careful monitoring of temperature ensures that properties such as color and gloss remain intact during curing.
How to Achieve a Smooth Surface Finish
A smooth finish is often desirable for aesthetic and functional reasons. To achieve this, consider the following tips:
- Consistent Application: Ensure that the powder is applied evenly to avoid runs or sags.
- Pewter Touch-Up: Utilizing a compatible touch-up paint can address minor imperfections post-curing.
- Polishing: For enhanced gloss, consider polishing the finalized surface with a fine microfiber cloth.
Maintenance Tips for Powder Coated Surfaces
Maintaining the integrity of powder-coated surfaces is relatively straightforward:
- Regular Cleaning: Use mild soap and water to clean surfaces, avoiding harsh chemicals that might degrade the coating.
- Inspect for Damage: Regularly check for chips or scratches and address them promptly to avoid corrosion.
- Avoid Abrasive Cleaners: Stick to soft sponges or cloths to prevent damaging the finish.
Future Trends in Powder Coating Technology
The future of powder coating looks promising, with technology evolving to meet industry demands for more efficient and eco-friendly solutions.
Advancements in Powder Coating Formulations
Innovations in chemical formulations have led to the development of powders that offer even greater attributes, such as:
- Higher Durability: Newer formulations boast enhanced durability against UV rays and chemicals.
- Heat-Resistant Powders: Formulations capable of withstanding higher temperatures are being increasingly sought after in automotive and industrial sectors.
- Textured Finishes: The availability of textured powders is on the rise, allowing for greater design versatility.
Eco-Friendly Innovations in the Industry
As sustainability becomes paramount, powder coating technology has responded with eco-friendly innovations, including:
- Water-Based Powders: Some manufacturers are developing water-based powder coatings that offer lower VOC emissions.
- Bio-Based Materials: Utilizing renewable resources for powder production promotes sustainability.
- Recycling Initiatives: The industry is exploring ways to recycle excess powder and improve powder recovery systems.
Market Outlook and Opportunities in Powder Coating
The powder coating market is projected to continue growing, driven by expanding sectors that recognize the benefits of durability and aesthetics. The global demand for powder coating is influenced by:
- Growing Automotive Industry: With more automotive manufacturers adopting powder coating, the sector continues to expand.
- Urban Development: Architectural projects demanding durable finishes are pushing the demand for powder-coated products.