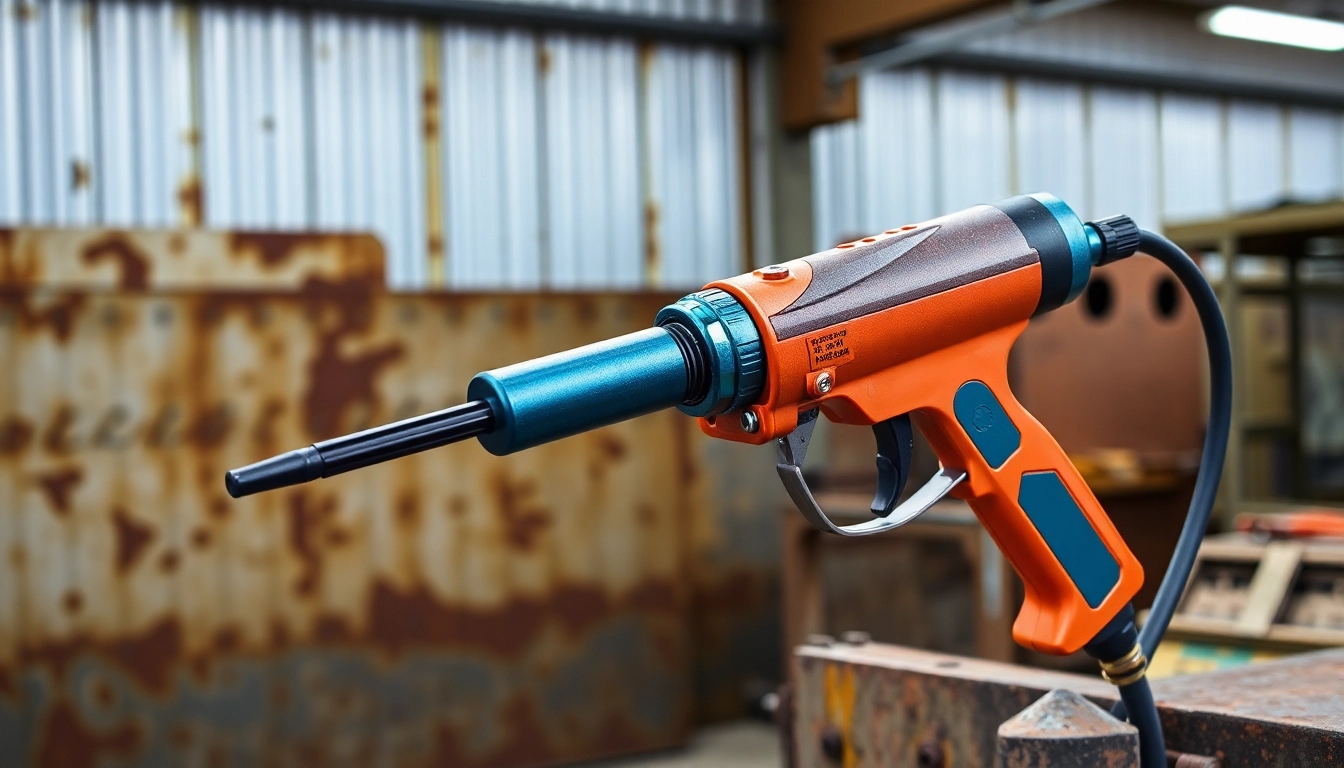
Introduction to Needle Guns
Needle guns, an essential tool in various industrial applications, are particularly valued for their ability to deliver effective surface preparation. This powerful tool, often termed a needle gun or needle scaler, is primarily used to remove rust, mill scale, and old paint from metal surfaces, making it indispensable in sectors such as automotive repair, shipbuilding, and metal fabrication. As the need for efficient surface preparation continues to grow, understanding the features, types, and best practices associated with needle guns becomes critical for professionals looking to maximize productivity and ensure quality results.
What is a Needle Gun?
A needle gun is a pneumatic or electric tool that utilizes a series of high-speed needles to create a rapid vibrating motion. This action effectively chips away at unwanted materials while being gentle enough not to damage the underlying metal surface. The key functionality of a needle gun lies in its mechanism, where compressed air, in the case of pneumatic versions, or electrical power, drives the needles at high beats per minute (BPM), often between 3,000 and 5,000 BPM. Such performance figures make needle guns remarkably effective for intensive cleaning applications.
Applications in Industry
Needle guns are widely utilized across various industries. Here are some notable applications:
- Automotive Repair: In automotive workshops, needle guns are frequently used to remove rust from chassis and bodywork, ensuring a clean and sufficient surface for painting and repairs.
- Shipbuilding and Maintenance: Marine engineers employ needle guns for hull preparation, effectively removing marine growth, rust, and old paint to maintain structural integrity and aesthetic appeal.
- Metal Fabrication: In fabrication settings, they are essential for surface preparation before welding to ensure proper adhesion and finish quality.
- Maintenance and Restoration: Needle guns are also employed in buildings for restoration work where intricate cleaning of metal fixtures and supports is required.
The Evolution of the Needle Gun
The origins of the needle gun trace back to the 19th century, where early models were primarily handheld mechanical devices. Modern advancements have seen the rise of pneumatic and electric needle guns that not only enhance ease of use but also improve performance. The evolution of materials has also played a pivotal role, with contemporary needle guns constructed from lightweight yet durable materials to enhance portability without compromising strength.
Types of Needle Guns
Pneumatic vs. Electric Needle Guns
The choice between pneumatic and electric needle guns largely depends on the application and workplace conditions. Pneumatic needle guns draw power from compressed air, making them suitable for extensive use in industrial environments where continuous operation is required. They tend to be more powerful and can often deliver higher BPM compared to electric models.
Conversely, electric needle guns are generally more portable and user-friendly, as they do not require a compressed air source. They deliver a significant amount of power sufficient for lighter applications and are ideal for mobile or smaller scale operations where space and accessibility are limited. When choosing between pneumatic and electric models, consideration should be given to workload, availability of compressed air, and personal comfort with handling the tools.
Choosing the Right Needle Gun for Your Project
Selecting the appropriate needle gun can significantly influence project outcomes. Here are some factors to consider:
- Project Scale: For large-scale industrial projects, a pneumatic needle gun may be more suitable due to its extended operation and power capabilities. For smaller tasks, an electric model may suffice.
- Surface Material: The type of metal being worked on will dictate the needle gun chosen; harder metals may require tools with stronger needles designed specifically for tougher applications.
- Safety Features: Consider models that offer safety features such as automatic shut-off or improved grip for operator comfort and safety during extensive use.
- Budget: Price can vary widely depending on model and features. It’s important to balance quality with cost, ensuring that the selected needle gun will perform efficiently for the intended use.
Popular Brands and Models
Several brands dominate the needle gun market, known for their advanced technology and reliability:
- Ingersoll Rand: Renowned for their high-performance pneumatic tools, their needle scalers are considered industry standards.
- JET: Offers a range of both pneumatic and electric needle scalers designed for heavy-duty applications.
- DEWALT: Known for robust electric tools, DEWALT’s needle guns are favored for their durability and user-friendly design.
- Chicago Pneumatic: Provides a range of needle scalers ideal for professional applications, known for efficient performance and ergonomics.
Technical Specifications
Understanding Power Requirements
Understanding the power specifications of needle guns is crucial for operational efficiency. Pneumatic models typically require a compressor capable of delivering a specific CFM (Cubic Feet per Minute) and PSI (Pounds per Square Inch). The general standard for pneumatic needle guns is around 6 CFM at 90 PSI.
Electric models will have their power consumption noted in watts, and it’s vital that the power supply can meet the equipment’s demand. Additionally, for both types, the needle count can also affect performance; a higher number of needles can hasten the surface area covered but may also lead to quicker wear.
Performance Metrics of Needle Guns
Several performance metrics should be evaluated when assessing needle guns:
- BPM (Beats Per Minute): The speed at which the needles vibrate has a direct effect on efficiency. Higher BPM often translates to faster material removal.
- Needle Gauge: Thicker needles can handle tougher materials but may require more power.
- Weight and Ergonomics: A well-balanced tool can help reduce operator fatigue during prolonged use.
- Sound Level: Noise levels, measured in decibels, are important as excessive noise can lead to hearing damage over time.
Maintenance and Durability
Regular maintenance is vital to the longevity of needle guns. Here are some suggestions:
- Regular Cleaning: Keep the needle tips clean and remove debris to prevent clogging and ensure optimal performance.
- Inspection: Regularly inspect the tool for wear and tear, particularly around the trigger, needle housing, and hose connections in pneumatic models.
- Lubrication: Follow manufacturer recommendations on lubrication to enhance the motion of internal parts, particularly in pneumatic models.
- Storage: Store needle guns in a dry, safe environment to protect from physical damage and moisture, which might rust parts.
Best Practices for Using Needle Guns
Safety Guidelines
Using needle guns effectively and safely requires adherence to best practices:
- Personal Protective Equipment (PPE): Always wear appropriate PPE, including eye protection, hearing protection, gloves, and respiratory protection if required, to safeguard against dust and particles released during operation.
- Proper Handle and Grip: Ensure a firm grasp on the tool to avoid slips and accidents. Ergonomic grips reduce the likelihood of fatigue.
- Follow Manufacturer Instructions: Adhering strictly to the user manual will avoid misuse and possible damage to the tool or injuries.
Optimal Techniques for Efficiency
To maximize the performance of needle guns, operators can apply several techniques:
- Angle and Motion: Use the needle gun at the correct angle to effectively chip away materials. A dynamic motion rather than a static one often yields better results.
- Surface Preparation: Ensure the surface is clear of larger debris to facilitate the needle gun’s work.
- Consistent Operation: Avoid stopping frequently during operation—consistency assists in smoother and more effective material removal.
Environmental Considerations
It’s crucial to consider environmental impacts when using needle guns. Projects should be planned to minimize dust and debris dispersion in sensitive areas. Additionally, appropriate disposal methods must be employed for materials removed, complying with local regulations regarding waste management. Beyond cleanliness, employing dust collection systems can help limit airborne particulates and improve workplace safety.
Conclusion and Future of Needle Guns
Innovations in Needle Gun Technology
The future of needle guns is promising, with technological advancements leading to enhanced performance and functionality. Developments in materials science are yielding needles that last longer and work more effectively. Additionally, integration with IoT technologies could allow for real-time monitoring of tool performance and maintenance needs, optimizing workflows and reducing downtime.
Trends in Surface Preparation Tools
The trend towards automation in surface preparation is notable, with needle scalers being developed that semi-automate tasks. This shift continues to reduce manual labor and improves consistency in surface preparation. Sustainability is another growing trend, with more manufacturers focusing on producing energy-efficient tools and lessening the environmental impact of surface preparation.
Final Thoughts on Needle Gun Usage
Needle guns remain critical tools for professionals involved in surface preparation across various industries. By understanding the intricacies of their operation and maintenance, and by staying updated on the latest technologies, operators can leverage needle guns to their full potential, leading to efficient, high-quality results in their work. Whether you are maintaining a fleet of vehicles, restoring a historic ship, or preparing surfaces for welding, the needle gun is an indispensable ally in achieving optimal results.