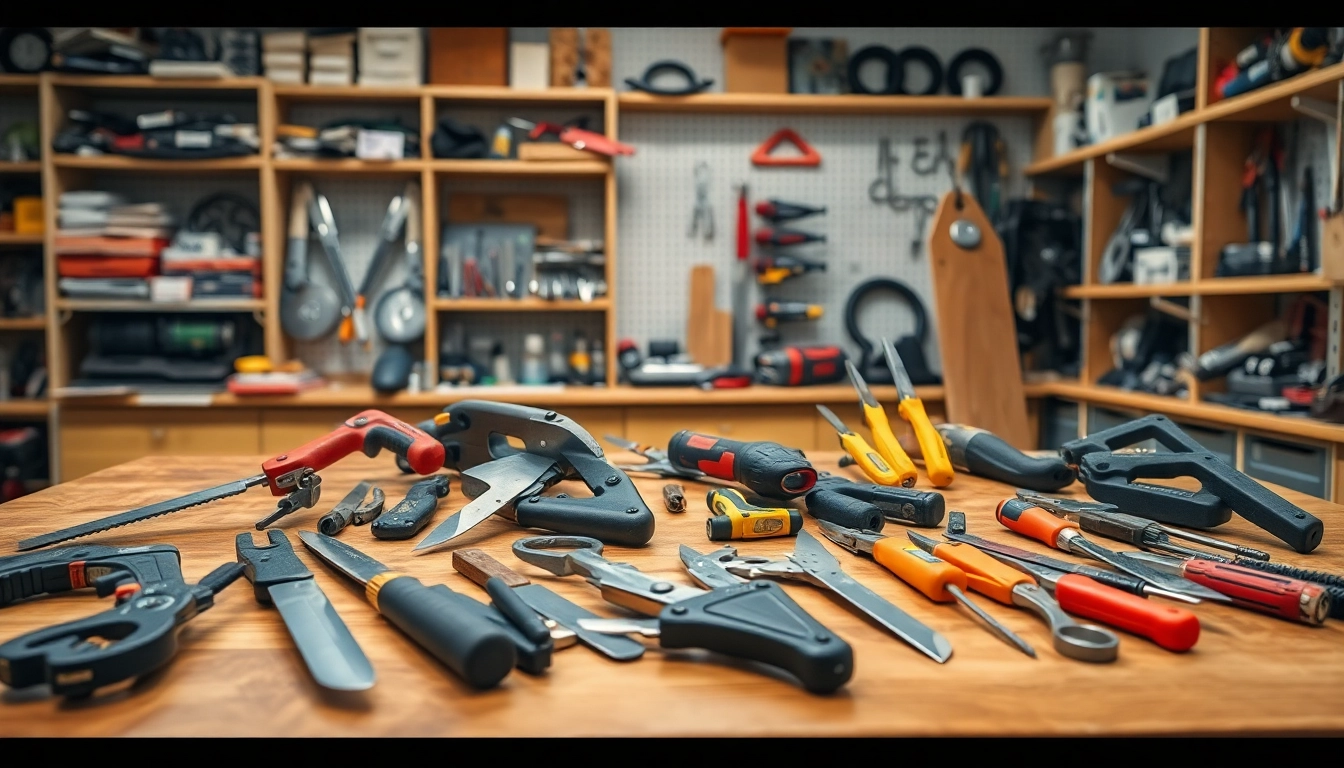
Introduction to Cutting Equipment
In various industries, the precision and efficiency of cutting processes are crucial. Whether in manufacturing, food processing, construction, or crafts, having the right cutting equipment can determine the quality of output and operational efficiency. Cutting equipment encompasses a wide range of tools and machines designed to slice, chop, shear, or otherwise divide materials into desired shapes or sizes. This article aims to give you a deep dive into cutting equipment, including its importance, types, applications, selection criteria, maintenance practices, safety measures, and technological advancements.
The Importance of Quality Tools
Quality cutting tools are essential given their direct impact on productivity and safety. High-grade tools enhance precision, reduce material waste, and minimize the physical effort required by operators. Furthermore, reliable equipment reduces the risk of accidents and injuries in the workplace, leading to a safer and more productive environment. In industries that rely on cutting equipment, such as manufacturing and culinary fields, the quality of the tools can influence the end product’s quality, ultimately affecting customer satisfaction and brand reputation.
Types of Cutting Equipment
Cutting equipment can generally be classified into two main categories: manual tools and powered machines. Each serves different applications and industries. Here’s a more detailed classification:
- Manual Cutting Tools: These tools require human effort to operate and include items like knives, scissors, shears, and hand saws. They are often used in settings like kitchens or small workshops.
- Powered Cutting Machines: These machines utilize electrical power or fuel to operate and are typically used in industrial applications. Examples include band saws, laser cutters, CNC machinery, and plasma cutting systems. Each type of powered machine is designed for specific materials and offers different levels of precision and operational speeds.
- Specialized Cutting Equipment: This includes equipment designed for specific materials or industries, such as concrete cutting saws, metal shearers, or food slicers. Such tools are crafted to meet the unique demands of different applications.
Common Applications and Industries
The usage of cutting equipment spans a multitude of industries:
- Manufacturing: Saws, scissors, and laser cutting machines are utilized for fabricating parts and components.
- Construction: Heavy-duty cutting tools are essential for cutting through materials like steel, concrete, and wood, aiding in structural development.
- Food Industry: Food preparation often requires specialized cutting equipment such as slicers and dicers to ensure hygiene and efficiency in food processing.
- Textiles: In the textile industry, cutting tools are vital for pattern-making and garment construction.
Choosing the Right Cutting Equipment
Selecting the appropriate cutting equipment is paramount for achieving desired results. There are several factors and best practices to consider during this process.
Factors to Consider
When determining the right cutting equipment for your needs, consider the following factors:
- Material Type: The material you’ll be cutting greatly influences equipment choice. Different tools perform better on wood, metal, paper, or fabric.
- Thickness and Volume: Evaluate the thickness of the materials and the volume of work. For heavy-duty cutting tasks, specialized power tools may be necessary.
- Precision Requirements: Some projects require high precision, which may necessitate more advanced tools such as CNC machines or laser cutters.
- Budget: Determine your budget. While investing in quality equipment can offer long-term savings, find the balance that ensures you do not overspend prematurely.
Best Practices for Equipment Selection
To further refine your selection process, here are additional best practices:
- Research various options and read user reviews to understand how specific tools perform in real-world applications.
- Consult with industry professionals or experienced colleagues who can provide insights based on their experiences.
- Consider the availability of after-sales support and maintenance services for the equipment you choose.
- Test equipment if possible; many retailers offer demo units or rental options that allow you to gauge their functionality before purchasing.
Resources for Further Research
Numerous resources can aid in your research when choosing cutting equipment:
- Professional trade associations often provide guidelines and resources for selecting cutting tools suitable for specific industries.
- Online forums and discussion groups can be beneficial in gathering experiences and recommendations from other users.
- Manufacturer websites frequently contain detailed specifications, user manuals, and application guides that can inform your purchasing decisions.
Maintenance and Care for Cutting Equipment
Proper maintenance is essential for longevity and performance efficiency of cutting equipment. Here are some routine practices and troubleshooting techniques.
Routine Maintenance Tips
To keep your cutting equipment in optimal working condition:
- Regular Cleaning: Dirt and debris can dull blades or damage components. Regularly clean your tools according to the manufacturer’s instructions.
- Lubrication: For machines with moving parts, ensure they are regularly lubricated to prevent wear and tear.
- Blade Sharpening: Dull blades lead to poor cuts and increased wear on equipment. Regularly sharpen or replace blades as needed.
Common Issues and Troubleshooting
Even the best cutting equipment may encounter issues. Here are common problems and their solutions:
- Inconsistent Cuts: This may indicate dull blades or misalignment. Regularly check blade sharpness and alignment settings.
- Excessive Vibration: This can be caused by loose components or an unbalanced load. Examine parts for tightness and ensure weights are distributed evenly.
- Overheating: This could result from prolonged use, insufficient lubrication, or wrong settings. Allow equipment to cool and assess if adjustments are needed.
Extending the Life of Your Equipment
To maximize the lifespan of your cutting equipment, consider the following practices:
- Store equipment in a clean, dry, and secure area to prevent damage.
- Train users on proper handling techniques to reduce the likelihood of accidental damage.
- Follow the manufacturer’s guidelines for usage and maintenance diligently.
Safety Practices When Using Cutting Equipment
Safety should always be a priority when using cutting tools. Here are some crucial safety practices to follow:
Essential Safety Gear
Always ensure proper safety gear is worn when operating cutting equipment, which may include:
- Protective Eyewear: To shield against flying debris or sparks.
- Protective Gloves: To prevent injuries when handling sharp tools.
- Hearing Protection: Necessary for loud machinery that produces high decibel levels.
Safe Handling Techniques
Implement safe handling practices to reduce the risk of accidents:
- Always follow the manufacturer’s instructions and safety guidelines when operating tools.
- Keep work areas well-lit and free of clutter to avoid trips and falls.
- Make sure that proper body positioning is maintained to avoid strain or injuries.
Emergency Procedures
In the event of an accident, having a clear set of emergency procedures is crucial:
- Ensure all users are aware of emergency shutdown procedures for machinery.
- Have first aid kits readily available and ensure all workers know their location.
- Conduct regular drills to ensure readiness in case of emergencies.
Advancements in Cutting Equipment Technology
As technology continues to evolve, the realm of cutting equipment has seen significant advancements. Here’s an overview of some of the latest innovations and future trends.
Innovative Tools and Features
Modern cutting equipment benefits from various innovative features that enhance functionality and user experience, including:
- Smart Technology: Many new machines come equipped with smart technology that allows for better accuracy, tracking usage patterns, and automatic adjustments.
- Energy-Efficient Models: Newer tools are designed with energy efficiency in mind, reducing operational costs while maintaining performance.
- Ergonomic Designs: Ergonomically designed tools help reduce user fatigue and improve comfort and control.
Impact of Technology on Efficiency and Accuracy
Technological advancements have revolutionized cutting equipment, allowing for:
- Increased speed in cutting operations, thus enhancing productivity.
- Higher levels of precision, resulting in cleaner cuts and better material utilization, leading to less waste and higher quality end products.
- The ability to automate tasks, reducing the need for manual labor and increasing consistency.
Future Trends in Cutting Equipment
The industry is likely to continue toward several key trends:
- Integration with IoT: More cutting equipment will likely be connected, allowing for data collection and real-time monitoring.
- Increased Customization: The ability to tailor machines based on specific needs will grow, catering to unique operational requirements.
- Advancements in Materials: New materials and coatings will enhance blade durability and performance.
In conclusion, selecting and maintaining quality cutting equipment, coupled with adherence to safety practices, is vital for any business aiming for efficiency and high-quality outputs. As technology continues to evolve, staying informed and adaptable will ensure you remain competitive in your industry.