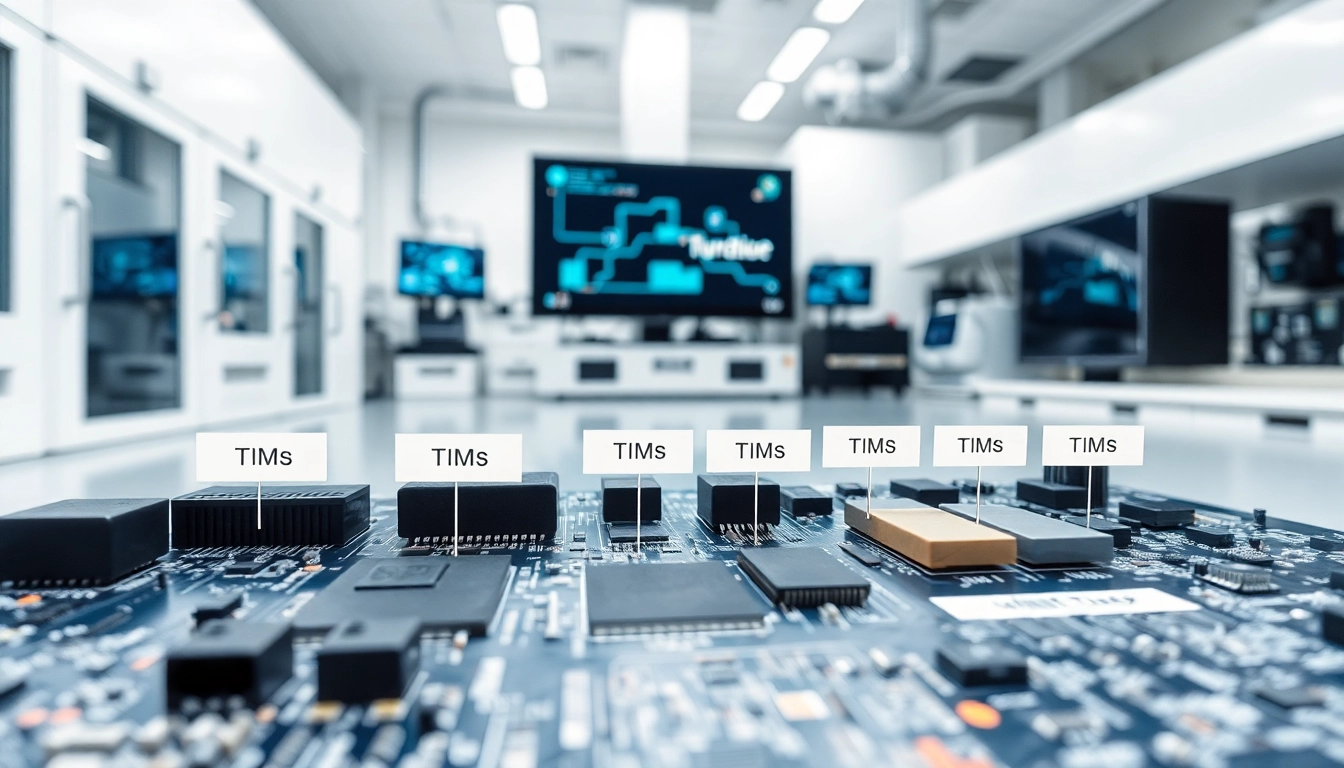
Understanding Thermal Management Materials
In today’s electronic-driven world, the effective management of heat is crucial for the performance, reliability, and longevity of electronic devices. This necessitates the use of thermal management materials, a category that consists of various products designed to dissipate excess heat generated by electronic components efficiently. From smartphones to electric vehicles, understanding thermal management materials enables designers and engineers to create more efficient and stable systems.
What are Thermal Management Materials?
Thermal management materials are specifically designed substances that facilitate thermal control within electronic applications. Their primary function is to enhance heat dissipation, thereby preventing overheating, improving performance, and ensuring safety in electronic assemblies. These materials can function in various forms, including thermal interface materials (TIMs), thermal pads, gels, and adhesives, each exhibiting unique characteristics suited for different applications.
Types of Thermal Management Materials
Thermal management materials come in multiple types, catering to distinct needs and specifications:
- Thermal Interface Materials (TIMs): Essential for efficient heat transfer between surfaces, TIMs fill microscopic gaps to enhance thermal contact. Examples include thermal pastes and greases.
- Thermal Pads: These soft, compressible materials conform to surfaces to provide efficient thermal conductivity while also offering insulation against electric current.
- Gap Fillers: Used where traditional TIMs cannot fill, gap fillers manage thermal energy transfer in larger heights and irregular shapes.
- Thermal Adhesives: These aid in both bonding and thermal transfer, often utilized in high-power applications where reliability is key.
- Thermal Gels: These materials provide excellent thermal conductive properties with a degree of malleability, making them suitable for various applications.
Key Applications in Electronics
Thermal management materials find extensive applications across several electronic domains:
- Consumer Electronics: Smartphones, laptops, and tablets utilize TIMs and thermal pads to manage heat generated during usage.
- Automotive: Electric vehicles benefit from thermal adhesives and gap fillers to ensure efficient cooling across battery components.
- Telecommunications: Network equipment relies on thermal management to maintain operational efficiency and prevent downtime.
- Industrial Applications: Heavy machinery that generates heat needs robust thermal solutions for reliable operation.
The Science Behind Thermal Management
Understanding the science of thermal management is vital for leveraging the full potential of thermal management materials.
Heat Transfer Mechanisms Explained
Heat transfer occurs through three primary mechanisms: conduction, convection, and radiation. In electronic applications, conduction and convection are most prominent. Conductive materials transfer heat through contact, while convection involves the movement of liquids or gases to distribute heat. Designers must consider these mechanisms when selecting thermal management solutions to optimize thermal performance effectively.
Importance of Thermal Interface Materials (TIMs)
Thermal interface materials are the backbone of effective thermal management. They significantly enhance thermal performance by bridging the gap between heat-generating components and heat sinks, thus minimizing thermal resistance. The effectiveness of TIMs depends on their thermal conductivity, compliance, and durability, making their selection a critical decision in any thermal management strategy.
Material Properties That Matter
When choosing thermal management materials, several key properties should dictate your selection:
- Thermal Conductivity: Measured in W/mK, higher thermal conductivity values indicate better heat transfer capabilities.
- Viscosity: This property affects application methods; lower viscosity allows for easier spreading.
- Thermal Stability: Materials must maintain performance over time in high-temperature environments.
- Electrical Insulation: Essential for preventing electrical shorts in electronic applications.
- Mechanical Compliance: The ability to conform to uneven surfaces ensures optimal thermal contact.
Choosing the Right Thermal Management Materials
Selecting appropriate thermal management materials is imperative for achieving optimal performance in electronic systems. A structured approach can help streamline this process.
Factors to Consider When Selecting Materials
To select the most suitable thermal management materials, consider the following factors:
- Device Specifications: Understand the heat generation and dissipation requirements of your devices.
- Operating Environment: Consider the environmental conditions, including temperature ranges and humidity.
- Mechanical Properties: Ensure the materials can withstand physical stress encountered in the application.
- Cost and Availability: Evaluate the cost-effectiveness and sourcing of materials to stay within budget.
Performance Metrics and Standards
Performance metrics such as thermal conductivity, dielectric strength, and hardness need to be evaluated against industry standards. Various test protocols, including ASTM and ISO standards, can provide benchmarks to assess material performance accurately.
Comparing Leading Brands and Products
Conducting a comparative analysis of leading brands can help inform your decision. Brands like Henkel, DuPont, and 3M offer a diverse range of thermal management solutions, each with distinct features and benefits. It’s essential to review product datasheets, technical specifications, and user testimonials to form a comprehensive understanding of what each product offers.
Best Practices for Implementing Thermal Management Solutions
After selecting the right materials, implementing them effectively is crucial for performance optimization.
Installation Techniques for Optimal Performance
Proper installation techniques can significantly impact the effectiveness of thermal management materials. Consider these best practices:
- Surface Preparation: Clean the surfaces thoroughly to remove dust, oil, or residues that may impede thermal contact.
- Pressure Application: Ensure that appropriate pressure is applied to TIMs to eliminate air gaps and maximize contact.
- Controlled Environment: Install materials in a controlled environment to prevent contamination or premature curing.
Troubleshooting Common Issues
Common issues that may arise include thermal performance degradation and mechanical failures. Regular inspections can help identify early signs of material failure, allowing for timely intervention.
Maintenance and Monitoring Strategies
Continuous monitoring of thermal performance can help ensure optimal functioning. Setting up temperature sensors and analyzing thermal imaging can provide valuable insights into the effectiveness of thermal management over time.
The Future of Thermal Management Materials
The landscape of thermal management is evolving, with new innovations emerging to meet ever-increasing demands.
Emerging Technologies and Innovations
Advancements in materials science are introducing highly efficient thermal management products. Innovations such as phase-change materials (PCMs) and advanced composites promise to improve thermal performance dramatically while lowering energy consumption. Research continues to explore nanomaterials and smart materials capable of adapting their thermal properties in real-time.
Sustainability in Thermal Management
Environmental concerns are prompting manufacturers to develop sustainable thermal management materials. Biodegradable TIMs and those made from recycled materials are gaining traction and can potentially reduce waste and carbon footprints within the electronics industry.
Market Trends and Growth Predictions
The global thermal management materials market is projected to grow as the demand for efficient electronic devices continues to surge. As industries adopt smarter technologies, the need for effective thermal solutions will only heighten. According to recent market studies, growth rates in the sector are expected to keep pace with advancements in electronics, with innovations driving a significant part of this expansion.