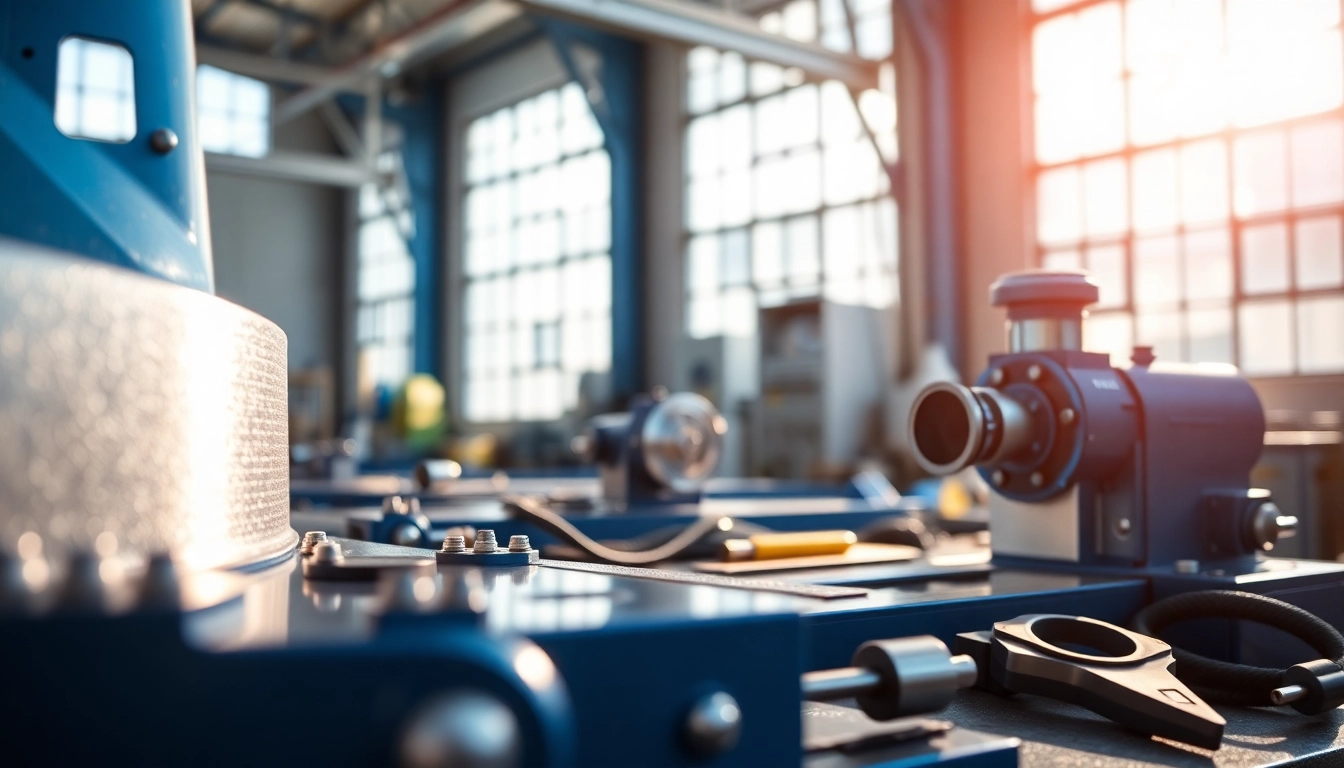
Introduction to Cutting Equipment
In the realm of industrial manufacturing, cutting equipment plays a pivotal role in ensuring efficiency and precision in various operations. These tools not only enhance the speed of production but also significantly improve the quality of the final products. Understanding cutting equipment, its types, applications, and technological advancements can empower businesses to optimize their processes and achieve greater productivity.
Definition and Importance of Cutting Equipment
Cutting equipment refers to the tools and machines used to slice, sever, or shear materials into desired shapes or forms. Essential across various sectors, these tools are integral to operations in industries such as manufacturing, construction, agriculture, and automotive. Their importance is underscored by their ability to improve material utilization, reduce waste, and enhance the overall quality of products.
Types of Cutting Equipment
The diversity of cutting equipment is vast, and each type serves specific purposes. Common types include:
- Mechanical Cutters: These include saws, shears, and laser cutters that physically alter the material.
- Thermal Cutters: Tools like plasma cutters and flame cutters utilize heat to melt and sever materials.
- Water Jet Cutters: Employing high-pressure water mixed with abrasives, these cutters are perfect for delicate materials requiring precision.
- CNC Machines: Computer-controlled equipment that automates the cutting process, ensuring high accuracy and repeatability.
Applications in Various Industries
Cutting equipment is utilized in a multitude of contexts:
- Manufacturing: In automotive and aerospace sectors, cutting tools are vital for creating precise components.
- Construction: From cutting steel beams to shaping concrete, cutting equipment ensures structural integrity.
- Textiles: Cutting tools are essential in the fashion industry for shaping fabrics with precision.
- Food Processing: Equipment like slicers and dicers is critical in managing food production efficiently and safely.
Key Features of High-Quality Cutting Equipment
Materials Used in Construction
Building robust cutting equipment involves using high-quality materials. Most cutting tools are made from:
- High-Speed Steel (HSS): Known for its hardness and durability, HSS is a common material in various cutting tools.
- Tungsten Carbide: Extremely hard and resistant to wear; it’s often used in blades and tips for precision cutting.
- Ceramics: Ideal for specific applications requiring a hardened edge that remains sharp over prolonged use.
- Composites: Used for lightweight and high-strength applications, especially in aerospace and automotive industries.
Technological Advancements
The cutting equipment landscape continually evolves, with innovations enhancing efficiency and capabilities. Key advancements include:
- Automation: The integration of AI and machine learning allows for smarter cutting processes that adapt to material variations.
- Laser and Plasma Technologies: Offering greater precision and flexibility compared to traditional cutting methods.
- Advanced Control Systems: Developing user interfaces that simplify operation and increase accuracy in cutting tasks.
Safety Features and Compliance Standards
Safety is paramount when operating cutting equipment. Essential features and standards include:
- Automatic Shut-Off: Disconnects power to the machine when unsafe conditions are detected.
- Protective Shields: Prevents accidental contact with blades and moving parts.
- Compliance with OSHA Standards: Ensures machines meet fundamental safety regulations in the workplace.
Choosing the Right Cutting Equipment
Assessing Your Needs and Applications
Selecting the right cutting equipment hinges on understanding specific operational requirements. Factors to consider include:
- Material Types: Differing materials require different cutting methods and equipment.
- Production Volume: High-volume operations may benefit from automated solutions, while smaller tasks can use manual tools.
- Precision Needs: Applications requiring intricate designs should prioritize equipment known for accuracy.
Top Brands and Models
Several manufacturers dominate the cutting equipment market, renowned for their quality and innovation. Notable brands include:
- Haas Automation: Known for their CNC machining centers, offering high precision and reliability.
- Lincoln Electric: Offers state-of-the-art welding and cutting products, especially in thermal cutting.
- Hypertherm: Specializes in advanced plasma cutting systems, known for their performance and ease of use.
Cost Considerations and Budgeting
When investing in cutting equipment, budgeting plays a crucial role. Consider the following:
- Initial Costs: Outlays for purchasing equipment vary significantly based on type and brand.
- Operational Costs: Maintenance, power consumption, and parts replacement should factor into long-term budgeting.
- Return on Investment (ROI): Evaluate how increased efficiency and quality can offset costs in the long run.
Best Practices for Using Cutting Equipment
Operational Techniques for Precision
To maximize the effectiveness of cutting equipment, employ best practices:
- Proper Setup: Ensure that equipment is calibrated according to manufacturer specifications before use.
- Consistent Maintenance: Regular checks on blades, components, and safety features help maintain precision and safety.
- Skilled Operatives: Training staff on best practices improves efficiency and minimizes errors.
Maintenance Tips for Longevity
Keeping cutting equipment in optimal condition extends its lifespan:
- Regular Cleaning: Debris and residue can affect performance; clean machines after each use.
- Oil and Lubricate: Regularly lubricate moving parts to prevent unnecessary wear and tear.
- Professional Inspections: Schedule periodic assessments by certified technicians to catch potential issues early.
Common Mistakes to Avoid
Avoiding pitfalls can significantly enhance productivity:
- Ignoring Safety Procedures: Prioritize safety training and adherence to operational guidelines.
- Overlooking Equipment Limits: Be aware of operational boundaries, such as material thickness and hardness.
- Neglecting Documentation: Keep logs of maintenance, operations, and any adjustments made for future reference.
The Future of Cutting Equipment
Emerging Technologies in the Field
The future of cutting equipment is promising, with several emerging technologies on the horizon:
- 3D Cutting Technology: Integrating 3D printing with traditional cutting methods for enhanced design flexibility.
- Smart Machines: IoT-enabled cutting equipment that sends real-time data for performance monitoring and predictive maintenance.
- Advanced Materials: Researching metals with self-healing properties and other innovative materials that improve cutting efficiency.
Sustainability and Eco-Friendly Innovations
With increasing global emphasis on sustainability, cutting equipment manufacturers are innovating to reduce environmental impact:
- Energy Efficient Machines: Development of cutting tools that consume less power during operation.
- Recyclable Materials: Creating cutting tools made from materials that can be fully recycled promotes sustainable practices.
- Waste Reduction Techniques: Innovations that minimize waste during the cutting process by optimizing material use.
Market Trends and Predictions
Analysts predict several noteworthy trends in cutting equipment:
- Increased Automation: More industries are expected to adopt CNC and robotic cutting technologies for efficiency.
- Integration of AI: Artificial intelligence will enhance decision-making in cutting processes, leading to improved quality and reduced downtime.
- Global Market Growth: The demand for advanced cutting equipment is projected to increase, driven by rising industrial activities worldwide.