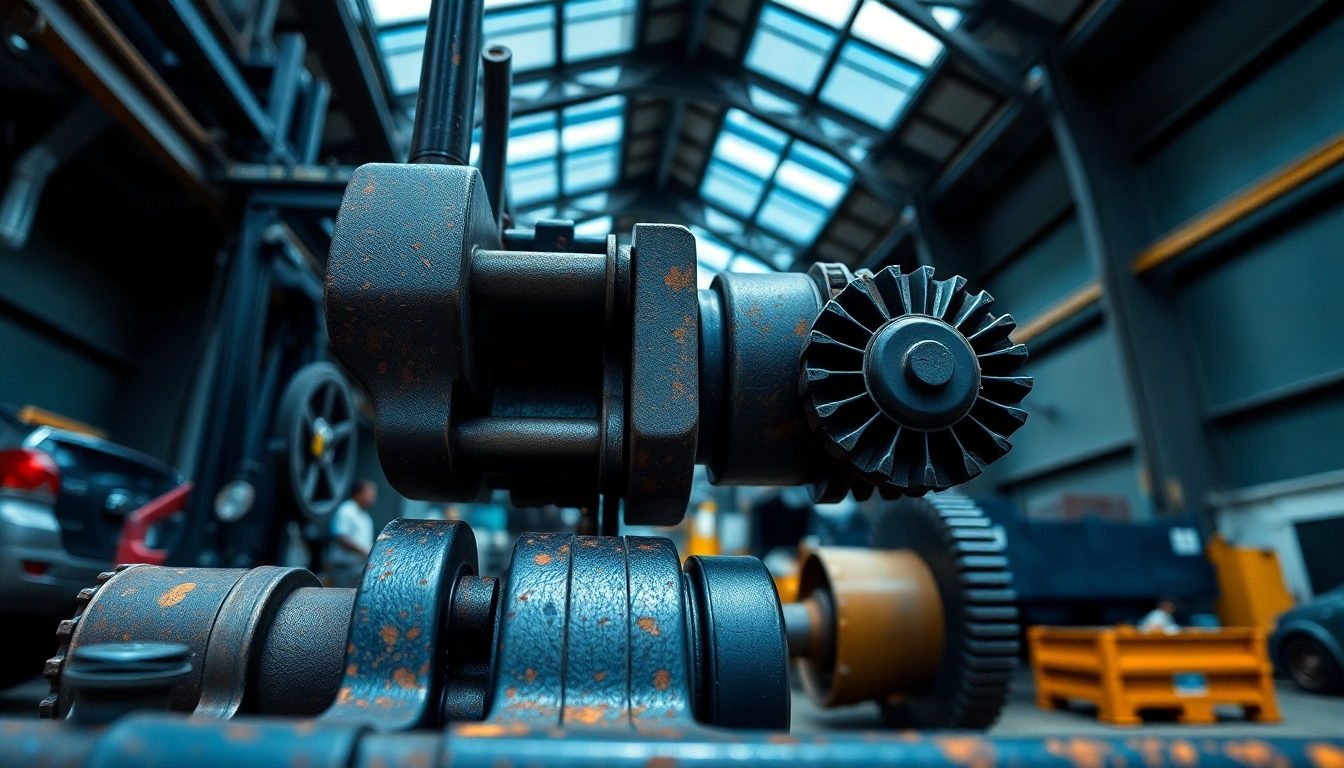
Understanding Liquid Packaging Machines
Liquid packaging machines are essential equipment in various industries, from food and beverages to pharmaceuticals and chemicals. These machines specialize in efficiently packaging liquids, ensuring minimal waste and optimal product safety. As businesses strive for efficiency and cost-effectiveness, the significance of selecting a reliable Liquid Packaging Machine Supplier becomes paramount.
Types of Liquid Packaging Machines
There are several types of liquid packaging machines, each designed to cater to specific product forms and industry requirements. Understanding these machines will allow businesses to make informed decisions tailored to their needs:
- Filling Machines: These machines dispense liquids into containers. They can be categorized further into sub-types such as volumetric, gravimetric, and overflow fillers.
- Capping Machines: Post-filling, these machines securely seal containers to prevent leaks and contamination.
- Labeling Machines: Essential for product identification and branding, these machines apply labels to containers with precision.
- Palletizing Machines: These systems arrange packaged goods onto pallets for efficient storage and transportation.
Key Features to Consider
Selecting a liquid packaging machine shouldn’t be based solely on the price; several critical features need consideration:
- Speed: The throughput capacity determines how many units can be filled, capped, and labeled in a given time.
- Precision: Accurate filling and capping reduce overflow and spillage, leading to cost savings.
- Flexibility: Machines that can handle various container sizes and types offer greater versatility.
- Ease of Use: User-friendly interfaces can reduce training time for employees and decrease operational errors.
- Maintenance Requirements: Consideration of maintenance frequency and part availability is crucial for minimizing downtime.
Benefits of Automating Packaging Processes
Automating packaging processes comes with a myriad of benefits that can drastically improve operational efficiency:
- Increased Efficiency: Automation significantly speeds up packaging processes, allowing companies to meet high demand without sacrificing quality.
- Reduced Labor Costs: By minimizing labor, companies can reallocate resources to other vital areas of the business.
- Consistency: Automated systems ensure consistent quality across products, which is crucial for brand integrity.
- Enhanced Safety: Machines reduce the risk of workplace injuries associated with manual packaging processes.
- Trackability: Many modern machines come equipped with technology that provides real-time data tracking and analysis.
How to Choose the Right Supplier
Choosing the right liquid packaging machine supplier is vital for the long-term success of your packaging operations. Here are key factors to evaluate:
Evaluating Supplier Credentials
In today’s competitive market, suppliers should meet several standards to be considered reputable:
- Industry Reputation: Research online reviews, testimonials, and case studies from other businesses.
- Experience: A supplier with extensive experience in your specific industry can offer better insights and solutions.
- Quality Assurance: Verify the supplier’s commitment to quality through certifications and compliance with industry standards.
Looking for Custom Solutions
Each business has unique packaging needs; finding a supplier that offers customization options can be a game-changer:
- Tailored Machinery: Suppliers willing to design machinery tailored to specific requirements can enhance efficiency.
- Integration Capabilities: Ensure they can provide machines that integrate seamlessly with existing systems.
Understanding Pricing and Maintenance
Beyond the initial purchase price, understanding the total cost of ownership is crucial:
- Initial Costs: Compare quotes but consider the features included in those prices.
- Operating Costs: Review energy consumption, labor requirements, and maintenance intervals to assess long-term expenses.
Industry Applications for Liquid Packaging Machines
Liquid packaging machines find applications across various sectors. Here’s a breakdown of the primary industries utilizing these machines:
Food and Beverage Industry
This sector heavily relies on liquid packaging machines for products ranging from beverages to sauces. Machines in this industry must adhere to strict health and safety regulations, ensuring that packaging does not compromise product quality:
- Beverage Filling Machines: These machines precisely fill bottles or cans with a range of liquids, from soft drinks to juices.
- Condiment Filling: Automatic machines handle viscous liquids like ketchup or mayonnaise with ease.
Pharmaceutical Sector
The pharmaceutical industry requires highly accurate and sterile conditions for packaging. Liquid packaging machines for this sector often include features like:
- Cleanroom Compliance: Many machines are designed to operate in controlled environments to meet health safety regulations.
- Robust Verification Systems: These help ensure dosing precision and product integrity.
Chemicals and Cosmetics
In the chemical and cosmetics industry, liquid packaging machines must handle a range of substances with varying viscosities:
- High-Capacity Machines: Often needed for bulk cosmetic products or industrial liquids.
- Custom Solutions: Many suppliers offer customized packaging solutions to handle specific chemical formulations.
Maximizing Efficiency with Advanced Machinery
Investing in advanced liquid packaging machinery pays dividends in increased operational efficiency:
Integrating Technology in Packaging
Modern machines are increasingly incorporating technology to streamline operations. Considerations include:
- IoT Capabilities: Internet of Things (IoT) technology allows for real-time monitoring and adjustments.
- Data Analytics: Analyze performance metrics to identify areas for improvement.
Continuous Improvement Strategies
Fostering an environment of continuous improvement can lead to sustained operational profitability:
- Regular Training: Keep staff updated on machine operations and maintenance practices.
- Feedback Mechanisms: Create channels for employees to suggest improvements to existing processes.
Training and Support from Suppliers
Partner with suppliers that offer robust training and ongoing technical support:
- On-Site Training: Many suppliers provide on-site training to ensure your team understands all machinery aspects.
- Technical Support: Ensure you have access to support in case of mechanical failures or questions about machinery.
Case Studies: Success Stories from Leading Suppliers
Learning from real-world applications gives invaluable insights into the effectiveness of liquid packaging machines:
Real-World Applications and Outcomes
Consider XYZ Corporation, a mid-sized beverage producer. By switching to an automated filling machine, they achieved:
- 30% Increase in Production: The switch boosted their packaging speed significantly.
- Reduction in Product Waste: Fewer spills and overfills due to accurate measurement capabilities resulted in considerable savings.
Feedback from Industry Professionals
Industry experts emphasize the importance of aligning machinery capabilities with product requirements. Jane Doe, a production manager at a leading cosmetics firm, stated, “Using machines designed for our specific formulations has led to fewer issues and smoother operation.”
Future Trends in Liquid Packaging
The future of liquid packaging is likely to be shaped by sustainability and technological advancements:
- Sustainable Materials: There’s increasing pressure to use eco-friendly packaging materials.
- AI and Automation: Industry experts predict that AI will play a pivotal role in optimizing packaging processes.