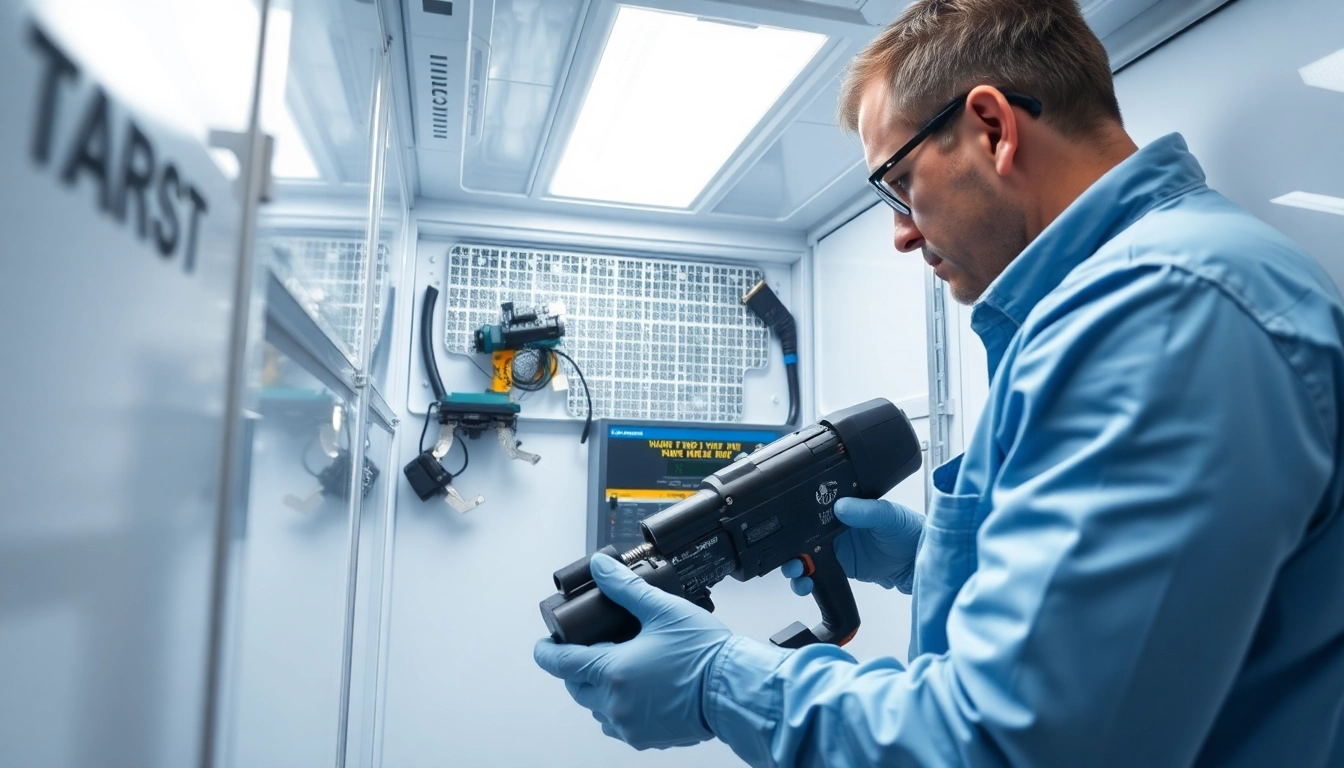
Understanding Walk In Freezer Repair Needs
In the world of commercial refrigeration, a walk-in freezer is a vital asset for businesses in various sectors, including food service, retail, and pharmaceuticals. When these units malfunction, it can lead to significant operational disruptions and financial repercussions. Understanding the common issues that necessitate walk in freezer repair is crucial for maintaining the efficiency and functionality of your business. Below is a comprehensive exploration of the common shortcomings in walk-in freezers, when to seek professional assistance, and the importance of routine maintenance.
Common Issues Leading to Repairs
Walk-in freezers are complex systems that can encounter a multitude of problems, each affecting their performance. Some of the most prevalent issues include:
- Temperature Fluctuations: One of the primary signs of a failing walk-in freezer is inconsistent temperature. This issue can stem from a malfunctioning thermostat, dirty condenser coils, or a faulty compressor.
- Excessive Frost Build-Up: Frost build-up can restrict airflow and decrease refrigerator efficiency. It often results from high humidity levels or poor door seals that allow warm air to enter the unit.
- Strange Noises: Unusual sounds such as grinding or hissing may indicate mechanical failures within the compressor or fan motor.
- Electrical Issues: Constant tripping of circuit breakers or blown fuses can signify electrical problems, potentially indicating that the components need professional assessment.
When to Call a Professional
While some minor issues can be fixed with DIY approaches, knowing when to bring in a professional is essential for preventing further damage. Signs that it’s time to call an expert include:
- Persistent temperature issues that do not resolve with basic troubleshooting.
- Frequent breakdowns or malfunctions that seem to recur within a short timeframe.
- Presence of unusual noises or vibrations that were not previously experienced.
- Unexplained increases in energy bills, which may indicate inefficiencies in the system.
Importance of Regular Maintenance
Maintenance plays a crucial role in extending the lifespan of walk-in freezers and preventing costly repairs. Regular inspection and servicing can identify potential issues before they escalate. Key maintenance tasks include:
- Cleansing condenser and evaporator coils to boost energy efficiency.
- Inspecting and replacing worn door gaskets to ensure proper sealing.
- Periodically checking refrigerant levels and compressors.
- Conducting temperature and performance tests to confirm the operational integrity.
By committing to a routine maintenance schedule, businesses can maintain efficiency, reduce operational costs, and enhance the longevity of their equipment.
Choosing the Right Repair Service
When it comes to selecting a repair service for walk-in freezers, it is vital to choose a reputable provider to ensure quality service. Here are essential steps to guide your decision-making process:
Identifying Qualified Technicians
Ensuring that the technicians you choose are certified and experienced in working with commercial refrigeration systems is paramount. Look for qualifications such as:
- Relevant Certifications: Technicians should have certifications from recognized industry bodies demonstrating their expertise in refrigeration systems.
- Experience: Providers with years of experience can often diagnose and resolve issues more effectively.
- Insurance: A credible service company should have the necessary insurance cover to protect both their technicians and your property.
Evaluating Service Reviews and Ratings
In the digital era, customer reviews are invaluable resources for assessing the reliability of a service provider. Consider the following:
- Online Reviews: Platforms like Google Reviews and Yelp can offer insights from previous customers about their experiences.
- Third-Party Ratings: Checking ratings from entities like the Better Business Bureau can assist in identifying reputable companies.
- Recommendations: Asking for referrals from fellow business owners can lead you to trustworthy service providers.
Comparing Costs and Services Offered
While cost should not be the sole determining factor, it is an essential consideration. Obtain quotes from several companies to benchmark pricing, but also ask about what services are included:
- Service Details: Understand the specific repairs and maintenance included in a quote to avoid hidden fees.
- Warranties: Ask if they offer warranties on their services, ensuring reliability and peace of mind.
- Availability: Check if they provide emergency services, as equipment failure can happen at any time.
DIY Tips for Basic Walk In Freezer Maintenance
For some routine tasks, business owners may choose to handle minor maintenance themselves. Below are essential tools and guidelines for maintaining your walk-in freezer efficiently.
Essential Tools You Need
To properly maintain your walk-in freezer, having the right tools is crucial. Basic equipment includes:
- Thermometers to monitor the temperature.
- Cleaning supplies for condenser and evaporator coils.
- Basic hand tools (screwdrivers, wrenches) for tightening and replacing components.
- Vacuum for cleaning dirt and debris from vents and coils.
Step-by-Step Maintenance Guide
Daily maximum efficiency can be achieved by adhering to a step-by-step maintenance guide:
- Check Temperature Settings: Daily, ensure that the temperature settings are appropriately adjusted according to your storage needs.
- Clean Coils: At least once a month, clean your condenser and evaporator coils to eliminate dust and debris buildup.
- Inspect Gaskets: Monthly, check door gaskets for wear and tear and replace them if necessary to maintain airtight seals.
- Monitor Performance: Regularly verify that fans are operational and that there are no strange noises during operation.
Preventative Measures to Avoid Breakdowns
Implementing preventative measures can minimize the risks of unexpected breakdowns. Key practices include:
- Training staff to properly operate and maintain the unit.
- Utilizing monitoring systems to alert you to temperature changes or malfunctions.
- Scheduling routine check-ups with a professional service provider.
Understanding Costs Associated with Repairs
When considering walk-in freezer repair, understanding the potential costs is fundamental. Numerous factors can influence the total expenditure on repairs and maintenance.
Factors Influencing Repair Costs
Repair costs can vary significantly based on multiple conditions, including:
- Severity of the Issue: Simple fixes such as replacing a contactor will be less expensive than replacing major components like the compressor.
- Service Call Fees: Many companies charge a service fee for the technician to visit your location, which can vary by region.
- Parts Required: The cost of replacement parts directly impacts service fees – some components are more costly than others.
Comparative Analysis: Repair vs Replacement
Business owners often grapple with deciding whether to repair or replace malfunctioning equipment. Here are some points of consideration:
- Age of Equipment: If the unit is older than 15 years and requires costly repairs, replacing might be more viable.
- Frequency of Repairs: If repairs are recurrent, invest in a new unit to avoid compounding repair costs.
- Efficiency Gains: New models often come with better energy efficiency ratings, leading to substantial savings in the long run.
Insurance Considerations for Commercial Units
Understanding your insurance coverage is crucial when it comes to repair costs for commercial units. Some considerations include:
- Types of Coverage: Ensure that your policy covers appliance repairs and damages.
- Documentation: Keep thorough records of maintenance and repairs, as insurers may require this information when filing claims.
- Choosing to Comply: Understanding policy limits and deductibles will aid in cost management during repair situations.
Future Trends in Walk In Freezer Technology
Embracing advancements in technology can ensure that your walk-in freezer operates at both high efficiency and reliability. Several trends are emerging in the commercial refrigeration landscape that can shape the future of these systems.
Innovations in Energy Efficiency
As energy costs continue to rise, walk-in freezer manufacturers are focusing on energy-efficient models featuring:
- Improved Insulation: New materials enhance insulation effectiveness, reducing energy consumption.
- Variable Speed Compressors: These compressors adjust their speed based on cooling needs, resulting in less energy use.
- Integrated Smart Technology: Energy monitoring systems allow business owners to optimize energy use and detect issues before they escalate.
Smart Features for Monitoring Performance
Modern walk-in freezers are increasingly being outfitted with smart technology, enabling effortless monitoring and improved reliability:
- Remote Monitoring: Business owners can now track temperature and performance through mobile applications.
- Automated Alerts: Many devices can send real-time alerts if temperature thresholds are breached, allowing for prompt action.
- Data Analysis: Advanced systems can analyze performance data to suggest maintenance schedules and predict potential failures.
Adjustments to Regulatory Standards and Compliance
Changes in regulations can impact how businesses manage their refrigeration equipment. Staying abreast of these updates is essential:
- Environmental Regulations: Increasingly strict regulations regarding refrigerants and emissions may require businesses to upgrade old systems.
- Health Standards: Compliance with health and food safety standards can influence walk-in freezer design and functionality requirements.
In conclusion, effective management of walk-in freezer functionality hinges on understanding the potential issues, timely professional intervention, and embracing regular maintenance practices. With the right knowledge and resources, businesses can ensure their equipment remains operational, optimized, and compliant with industry standards.